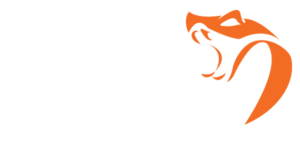
PROJECT BACKGROUND
As one of the largest powder coating companies in central NSW, this client’s high standard powder coating finish ensures that fabricated steel products can withstand years of outdoor exposure and usage. They offer abrasive blasting, zinc powder priming and powder coating services.
With the launch of BlastOne’s new SnakeBite nozzle, a large powder coating company wanted to test its efficiency. Together, we hosted a trial comparing a #7 BlastOne Ultra Tuff nozzle to the new SnakeBite Strike #10 nozzle. The trials focused on production rate and noise level. Additionally, abrasive consumption rates were also calculated to showcase overall cost.
PROJECT OBJECTIVES
Minimize overall dB levels
Achieve specified surface cleanliness and roughness standards
Ability to complete original project deadlines on-time
Generate considerable savings in production costs
Increase production capacity
Reduce abrasive consumption
RESULTS
BlastOne and the powder coating company conducted a study to determine whether the SnakeBite would reduce blasting noise without reducing productivity. Blasting a bin with large sides, no coating, here is how the #7 Ultra Tuff compared to the SnakeBite Strike:
Nozzle | Nozzle Pressure | Test Area | Blast Time | Blasting Speed | Sound Reading | |
#7 Ultra Tuff* | 115 psi | 1 m2 | 65 s | 592 ft2/hr (55 m2/hr) |
106 dBA | |
SnakeBite Strike | 102 psi | 1 m2 | 43 s | 893 ft2/hr (83 m2/hr) |
98 dBA |
*The Ultra Tuff Nozzle was worn close to a #8 nozzle
(Equipment used: 6001b Clemco Pressure Release Blast Pot, 390 cfm Diesel Compressor, No. 6 Blast Nozzle at 105psi at the nozzle)
Nozzle | #7 Ultra Tuff* | SnakeBite Strike |
Nozzle Pressure | 115 psi | 102 psi |
Test Area | 1 m2 | 1 m2 |
Blast Time | 65 s | 43 s |
Blasting Speed |
592 ft2/hr |
893 ft2/hr |
Sound Reading |
106 dBA |
98 dBA
|
*The Ultra Tuff Nozzle was worn close to a #8 nozzle
(Equipment used: 6001b Clemco Pressure Release Blast Pot, 390 cfm Diesel Compressor, No. 6 Blast Nozzle at 105psi at the nozzle)
Unfortunately, at the time, no sound readings were taken from further away, outside of the blast room. The difference in noise is even more obvious when you move further away.
Using the True Cost Abrasive Blasting Formula, we calculated the amount of abrasive used per square metre by each nozzle.
Nozzle | Consumption Rate* | Abrasive Purchase Cost Delivered | Abrasive Disposal Cost | Labor and Equipment Cost | Production Rate | Blasting Costs |
#7 Ultra Tuff | .48 t/hr | $695/t | $50/t | $150/hr | 592 ft2/hr (55 m2/hr) | $9.23 per m2 |
SnakeBite Strike | .48 t/hr | $695/t | $50/t | $150/hr | 893 ft2/hr (88 m2/hr) | $5.77 per m2 |
*Consumption rate is an assumption and will be kept constant.
Nozzle | #7 Ultra Tuff | SnakeBite Strike |
Consumption Rate* | .48 t/hr | .48 t/hr |
Abrasive Purchase Cost | $695/t | $695/t |
Abrasive Disposal Cost | $50/t | $50/t |
Labor and Equipment Cost |
$150/hr |
$150/hr |
Production Rate |
592 ft2/hr |
893 ft2/hr |
Blasting Costs |
$9.23 per m2 |
$5.77 per m2 |
*Consumption rate is an assumption and will be kept constant.
CONCLUSION
Our estimates show that the SnakeBite Strike is not only quieter than the #7 Ultra but it’s high productivity results in 37% less abrasive used per square metre. Over 1000 square metres, that is $3,460 back in your pocket! Almost covering the cost of the initial investment.
Blasting speed increased by 51% which is more than a day’s extra blasting each week.
Sound level was almost halved, which improved the surrounding environment for nearby workers and prevented disrupting workflows. While the SnakeBite Strike was in action, the noise was significantly reduced and a normal conversation (80dBA) could happen during blasting.
The SnakeBite Strike achieves over 50% more production than high performance #8 nozzles. The only #10 nozzle in the market that can be used for hand-held blasting for extended periods of time.
Experience the BENEFITS
THAN TUNGSTEN CARBIDE NOZZLES
THE SNAKEBITE DIFFERENCE
An entirely new operator experience. It feels different, it sounds different – and let’s face it, it looks fantastic! There is no other nozzle like it. The ultimate production tool that delivers contractors and asset owners lower noise, lower operator fatigue and improved project outcomes, ticking the box on the key challenges faced by the blasting industry today.
A SNAKEBITE NOZZLE FOR EVERY APPLICATION
Frequently Asked Questions
Does the reduced thrust compromise productivity compared to standard nozzles?
Productivity of the Flex is comparable with standard nozzles (same size, pressure, media) and the XQ is up to 25% more productive than standard nozzles of the same size. The reduced nozzle kick-back thrust – up to 45% – can actually increase productivity by reducing operator fatigue and enabling a high rate of productivity to continue throughout the shift…. and the #10 Strike (due to the larger orifice size) can increase hand-held blasting productivity up to 54%.
Is 1.25`` hose with a 750cfm compressor sufficient when using the SnakeBite Strike?
It depends on hose length. It is not recommended to use the Strike with a 1.25″ hose longer than 25 feet.Do I need any special equipment to get the SnakeBite noise and thrust reduction?
No, just screw the SnakeBite with the Silencer fitted into a contractor thread nozzle holder, set the pressure to 100psi and start blasting. Blasting noise will automatically be reduced by up to 16 dB and and you will immediately feel around 45% less nozzle thrust – there is nothing else you have to do.What if my nozzle isn't achieving a reduction of 16 dB?
Factors contributing to the optimal reduction in sound pollution include.- Nozzle pressure needs to be between 80-115 psi
- Blasting with lean abrasive flow increases noise
Adjusting these factors will have an effect on dB reduction.
How long will the nozzle last?
Expected wear-life for the SnakeBite is over 800 hours. This is 4x the life of a standard tungsten carbide nozzle.
CASE STUDIES
Contact BlastOne
We love to talk to customers and help them make the best decisions when purchasing equipment.
You can reach us via our Live Chat, Email, Phone, and Online Form.